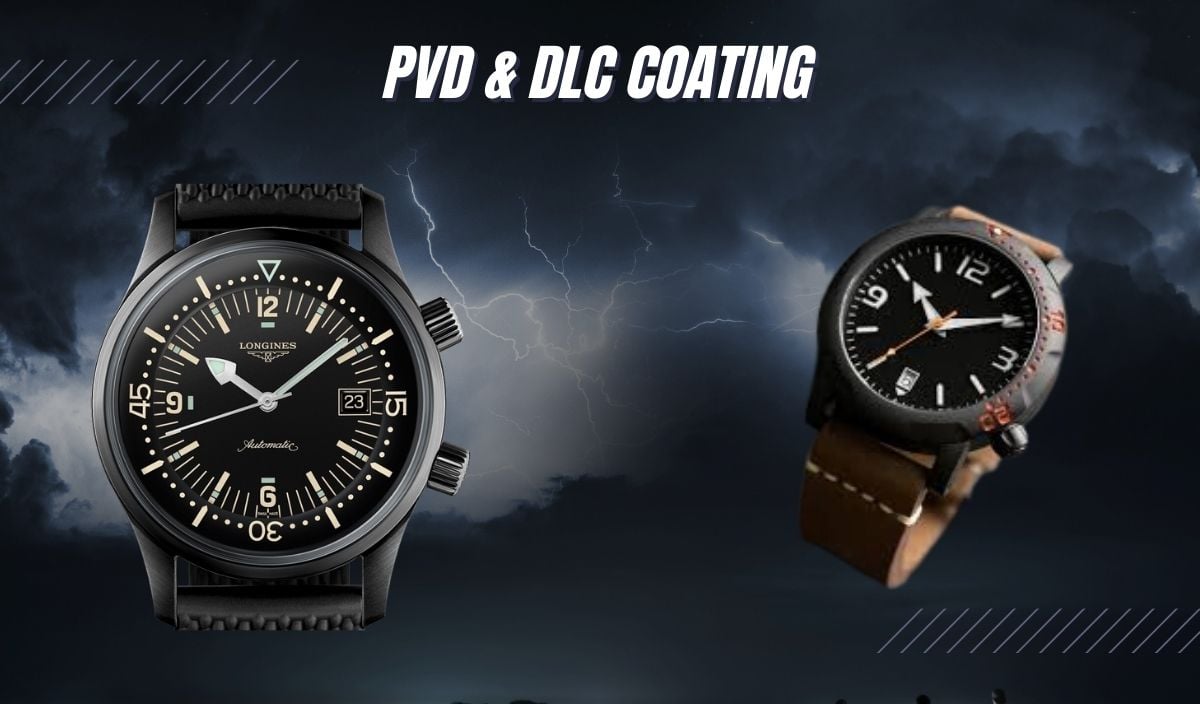
PVD & DLC Coating: EVERYTHING You Need To Know
In the realm of horology, watch enthusiasts and manufacturers are constantly seeking innovative ways to enhance the aesthetics and durability of timepieces. As technologies and manufacturing techniques evolve and become available in the watchmaking world, one such advancement in this field that has left a large footprint in the industry is the advent of watch coatings.
Among the most popular are Physical Vapor Deposition (PVD) and Diamond-Like Carbon (DLC) coatings. Both techniques have changed the watchmaking landscape, adding a blend of style, resilience, and functionality to modern timepieces.
In this article, we will delve into the technical aspects of PVD and DLC coatings, analyze their differences, highlight the pros and cons, and explore other types of watch coatings available in the market. Let’s dive in.
What is PVD Coating?
First, a description: Physical Vapor Deposition (PVD) is a thin-film coating process that involves depositing various materials on the surface of a watch in a controlled environment. This technique ensures a uniform and resilient layer, enhancing the watch’s appearance and performance.
PVD coating has gained immense popularity in recent years due to its versatility and ability to cater to various consumer preferences in both aesthetics and practical durability and wear.
Brands across the price and size spectrum from the micro level all the way to the top high-end have models making use of PVD in various applications. At its core, PVD coating enhances a watch’s looks and durability.
The PVD coating process is a meticulously controlled sequence of steps in manufacturing that transforms the watch’s surface, providing it with an additional layer of protection and aesthetic style (color, texture, etc.).
Cleaning and Preparation
Before the PVD coating process can begin, the watch components undergo a thorough cleaning. This step is crucial to remove any contaminants from the watch’s surface, ensuring optimal coating adhesion. A clean surface allows the coating to bond effectively with the timepiece, preventing any imperfections and enabling a uniform appearance.
Pre-Treatment
Once cleaned, the watch components go through a pre-treatment stage. In this step, the watch’s surface is prepared to increase its reactivity, enhancing the coating’s adhesion. Techniques like etching or ion bombardment are commonly employed in this pre-treatment phase to create a suitable surface for the subsequent deposition in the next step.
Deposition
The heart of the PVD coating process lies in the deposition stage. In a vacuum chamber, the watch components are exposed to a vaporized source material. The most commonly used materials in PVD coating are titanium nitride (TiN), zirconium nitride (ZrN), chromium nitride (CrN), and titanium carbonitride (TiCN). Each material offers distinct properties, including color, hardness, and scratch resistance.
The source material is vaporized using various methods, such as arc evaporation, where an electric arc is generated between the source material and an anode (usually made of copper). The electric arc heats the source material to extremely high temperatures, causing it to vaporize and condense on the watch’s surface.
Another such technique is sputtering, in which Argon gas (an inert gas that won’t chemically react with the target material) is introduced to the vacuum chamber. An electric field is applied, which ionizes the argon gas, creating a plasma. The plasma, containing positively charged argon ions, bombards the cathode surface with high energy.
As a result, atoms or ions from the cathode (target material) are sputtered or ejected from the surface, traveling through the vacuum chamber to ultimately condense on the watch surface, creating a thin film coating. In either case, this forms a thin film that adheres uniformly, providing the watch with the desired color and properties.
Post-Treatment
In some cases, an optional post-treatment stage may follow the deposition phase. This additional step further enhances the coating’s properties, such as hardness and adhesion. Post-treatment may involve exposing the coated watch to high temperatures or introducing other elements to improve its durability.
What is DLC Coating?
Often erroneously used interchangeably with PVD coating, Diamond-Like Carbon (DLC) coating is, in fact, a subset of PVD coating, which deserves special attention due to its unique properties.
DLC coatings are primarily composed of carbon, and as the name suggests, they possess diamond-like attributes, such as exceptional hardness and high resistance to abrasion, which are particularly useful in watchmaking for case durability and robustness.
The DLC coating process is similar to the standard PVD process, with some modifications to achieve the desired properties of the diamond-like carbon layer. Let’s examine this further.
Cleaning and Pre-Treatment
The watch components undergo thorough cleaning and pre-treatment, as with typical PVD coating, to ensure a clean and reactive surface for the DLC coating to be applied.
Deposition
Here in the deposition stage, we see the major breakaway from the standard PVD coating technique. With DLC coating, a carbon-based source material is used instead of the prior materials (ex: titanium nitride, zirconium nitride, chromium nitride, and titanium carbonitride).
The carbon material is vaporized using various methods, such as plasma-enhanced chemical vapor deposition (PECVD) or arc evaporation, as described prior. Upon vaporization, the carbon atoms are then ionized and accelerated towards the watch surface, creating a dense and complex carbon layer organized in an amorphous diamond-like structure, giving it diamond-like attributes without the high cost associated with natural diamond material.
Post-Treatment
DLC coatings often require additional post-treatment to improve their adhesion and hardness. Hydrogenation (introducing hydrogen atoms into the carbon matrix to occupy “vacant” sites within the amorphous carbon structure) is a common post-treatment method that enhances the DLC layer’s properties, making it more stable and less prone to delamination or cracking, as well as enhancing the coating’s ability to stay firmly bonded to the watch surface.
Differences Between PVD & DLC Coating
Composition
The primary distinction between PVD and DLC coatings lies in their composition. PVD coatings are made of various materials, which allows for a broader spectrum of color options and various degrees of hardness and durability of the finished product. On the other hand, DLC coatings are composed of amorphous carbon, making them exceptionally hard and durable, living up to the “diamond-like” nature as described.
Hardness
DLC coatings have a superior hardness compared to PVD coatings. Diamond-Like Carbon ranks high on the Vickers hardness scale, giving watches with DLC coating an added level of scratch resistance and protection against wear. Given the atomic structure of the material, it’s likely that DLC coating will have greater resilience and less tendency to flake or wear off the watch case overall, given the same duration of time.
Thickness
PVD coatings tend to be slightly thicker than DLC coatings, which can impact the final aesthetics of the watch. While PVD coatings are more visible, DLC coatings create a sleeker, smoother finish. And while we aren’t talking centimeters or inches of difference to the astute collector or those particular with watch thickness and measurements, it’s something to consider.
Color and Aesthetics
PVD coatings offer a wide range of colors, from gold and black to rose gold and bronze. These options cater to diverse consumer preferences and design choices. On the other hand, DLC coatings are predominantly known for their striking black appearance, though some variations like gray DLC also exist.
The stark black color gives DLC-coated watches a contemporary and sophisticated charm, appealing to many watch enthusiasts, and it’s often used in both sporty or military-leaning designs, which pair well with the material in aesthetic and functionality.
Pros & Cons of PVD & DLC Coating
Both PVD and DLC coatings have gained popularity in the watch industry for their versatility and ability to provide both functional and aesthetic benefits to watches. Let’s consider the pros and cons you might consider when choosing a timepiece with either treatment.
Pros
- Aesthetic Versatility: PVD coatings allow watchmakers to experiment with various colors, catering to a broader range of consumer preferences and style choices. The striking black appearance of DLC-coated watches exudes a contemporary and sophisticated charm, appealing to many watch enthusiasts.
- Improved Scratch Resistance: The additional layer provided by PVD coatings enhances a watch’s ability to withstand daily wear and tear, preserving its appearance over time. DLC coatings offer an unparalleled level of hardness and scratch resistance, ensuring the watch’s surface remains unmarred for extended periods.
- Cost-Effective: PVD coating is relatively more affordable than DLC, making it accessible to a broader audience of watch enthusiasts.
- Low Friction: The smooth surface of DLC coatings reduces friction, leading to enhanced performance and longevity.
Cons
- Limited Hardness: PVD coatings are not as hard as DLC, making them more susceptible to scratches and wear in the long run.
- Fading Over Time: While PVD coatings are durable, they may fade over extended periods, particularly when exposed to harsh conditions or regular friction.
- Limited Color Options: Unlike PVD coatings, DLC coatings are predominantly black (or gray), limiting the color choices available to consumers.
- High Cost: DLC coating is more expensive than PVD, which can influence the final retail price of DLC-coated watches.
Other Types of Watch Coating
Apart from PVD and DLC coatings, several other watch coating types are available in the market, each with its own distinct attributes.
Ceramic Coating
Explore the
Biggest Pre-Owned Collection of Luxury Watches
Ceramic coatings (ex: Cerakote) offer scratch, chemical, and corrosion resistance, as well as a broad range of color options. They are durable and maintain their appearance over time, making them a suitable choice for sports and dive watches, and provide additional personalized customization when added aftermarket.
Gold Plating
Gold plating provides an opulent appearance to watches, exuding a sense of luxury and prestige. However, it is less scratch-resistant compared to PVD and DLC coatings and may require re-plating over time (look to vintage gold-plated watches as examples). In practice, a layer of deposited gold plating can be much stronger and more resistant to wear than 12-karat or 14-karat gold watch cases at a more cost-effective price.
Rhodium Plating
Rhodium plating in watchmaking enhances a watch’s shine and offers increased scratch resistance. It is commonly used on white gold or silver watches to prevent tarnishing, though electroplating with Rhodium will not hide surface imperfections.
Conclusion
It would be no understatement to claim that watch coatings have transformed the world of watchmaking, offering a new blend of combined style and resilience since their introduction. PVD and DLC coatings, in particular, have gained immense popularity for their remarkable properties.
While PVD coatings provide a broader color palette and affordability, DLC coatings excel in terms of hardness and scratch resistance. Understanding these coating techniques empowers watch enthusiasts to make informed choices based on their preferences and intended use when ultimately deciding which watch to purchase.
Yet, regardless of the type of coating in question, these innovations highlight the dedication of watchmakers in their pursuit of crafting timepieces that not only stand the test of time but also exemplify aesthetic beauty and durability in use.
As technology continues to advance and materials improve, we can expect even more new technologies and watch coatings to emerge, further evolving the art of watchmaking. Such innovations ensure that watches remain timeless companions that complement both style and substance in our own watch-collecting journeys.
About Exquisite Timepieces
Established in 1998, Exquisite Timepieces is your one-stop shop for all things luxury watches! We are an authorized dealer for 60+ luxury watch brands including Omega, Hublot, Seiko, & Longines! We are proud to showcase one of the world’s largest pre-owned watch collections, including renowned brands like Rolex and Patek Philippe. Check out our brand new watch arrivals here and popular pre-owned listings here.